After only four months of using TALPA, a quarry operation was able to identify $12,500 in annual savings per ultra-class haul truck by using TALPA’s smartquarry suite. This customer leveraged TALPA’s off-the-shelf analytics models to optimize operator and machine performance.
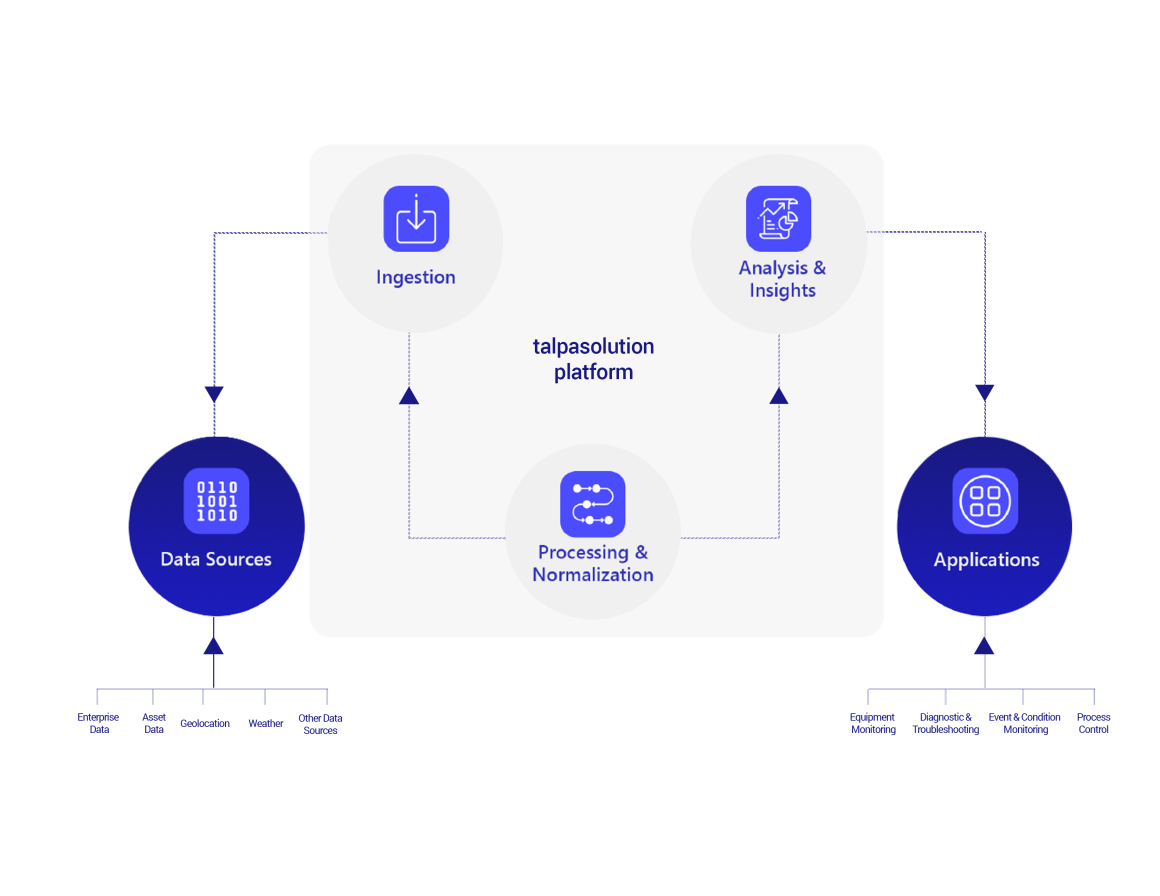
TALPA is an analytics software company, founded in 2016 in Essen, Germany. We provide predictive analytics applications for fixed and mobile assets, covering machinery and equipment in various industries, including mining, oil, gas, energy, logistics, and construction.
TALPA offers an industrial intelligence platform that uses real-time and historical data from machinery and equipment, as well as contextual information about the weather and the environment, to optimize operations for equipment operators and managers. The “end-to-end” data capture and analytics solution helps to prevent unscheduled downtime, extend the lifespan of machinery, and improve equipment utilization grade throughout the whole product lifecycle.
TALPA’s unique business model revolves around strategic partnerships with mining companies and OEMs to access large data sources, industry expertise, and deployed assets. We leverage our partners’ expertise to identify industry challenges and develop relevant applications that address specific pain points and enable new data-driven business models and revenue sources as well as operational performance improvement.
Overview
The procurement of mining machines, their regular substitution and maintenance are one of the major items in the project structure. Consumables, such as fuel and tires, also contribute to high numbers. Therefore, the average utilization rate of 69% across mining fleets, as well as rising operating costs, are deemed unacceptable, and the miners are seeking ways to improve their figures by implementing innovative digital solutions.
A global leader in the quarry industry recently selected TALPA‘s smartquarry suite to improve OEE and reduce unnecessary waiting time and related spending. TALPA, capable of analyzing any mining operation, identified the root causes of the operational losses. During a 4-month trial phase, our data scientist addressed the issue effectively. The company proactively delivered more than $12,500 in annual cost reductions and nearly 28% more operational output for the ultra-class haul and load operation. These results convinced the customer to scale TALPA‘s smartquarry solution across its whole fleet on US-sites.
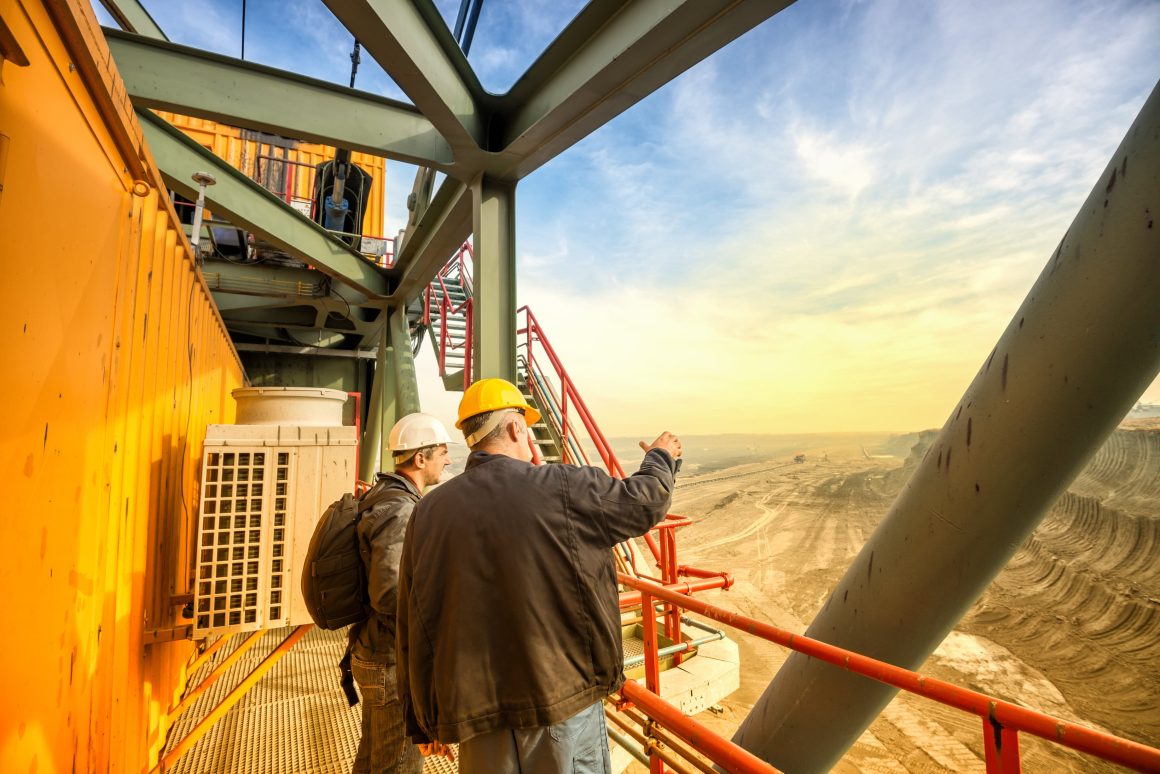
Challenge
In the face of increasing economic and environmental pressure on fleet operators, limited communication with operators can create inefficiencies in scheduling and managing the workflow, leading to extra trips, more time spent on administrative tasks, and less time spent on revenue-generating activities.
As a consequence, the quarry industry needed to reduce the variability and the unknowns of the mining process to make effective fleet management simpler. This is why a global leader in the quarry industry decided to adopt a proactive approach to address these complexities.
As the fleet operator continued to increase the number of ultra-class haul trucks in the fleet over the past few years, the operations team started seeing a drastic decrease in OEE. Based on a new quarry layout, the quarry operator intended to achieve an increase in productivity of 15-25%. This is where talpasolutions was consulted to help.
Solution
Built with MINERS for MINERS, the smartquarry suite solves industry-specific problems and delivers value quickly. Using the smartquarry suite has improved key processes throughout its workflow, delivering a clear understanding of how its operations were performing and where they could be improved.
smartquarry empowers the quarry operator to track and manage all his machines from different OEMs in one system, freeing employees who were previously tied up with low-value tasks to play a key role in driving revenue-building opportunities forward. The customer leveraged smartquarry’s
deep capabilities to boost its productivity:
- Improved fleet scheduling and detection of inefficiencies such as idle and long waiting times at loaders and crushers through detailed cycle and route analyses.
- Reduced wear of machines through pothole detection tools and concise mass handling.
- Mass flow assessments for both efficiency and cost analyses for overburden and multiple grades of aggregate using a uniform OEM-agnostic payload metering system.
- Simplified and introduced smarter purchasing of machines by comparing operational KPIs of various manufacturers.
- Reduced diesel consumption by 20% through dedicated OEM-agnostic consumption analysis applied to mass flows, various machine types, and equipment configurations.
- Increased mass flow by 28% and an increase in OEE through the identification of inefficiencies and improved HEX and OHT setups.
- Reduced administrative burden by integrating all pertinent data into one application.
- Boosted productivity and job satisfaction by automated shift, days, weekly and monthly reporting, and intuitive software usability.